The art of cutting and polishing gemstones hasn’t changed much over thousands of years. Of course, modern machinery has made the process quicker, but the creation of a magnificent gemstone from a rough block still requires a steady hand and an eye for excellence.
Cutting a gemstone
When cutting a gemstone the shape of the finished stone is chosen. This is nearly always an oval but may be more irregular shapes.
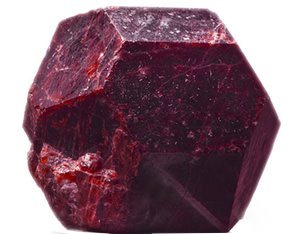
Gemstones cut by master jewellers
The shape is then drawn on the flattest side of the stone using a pencil.
A saw is used to trim away excess edges. The saws used have diamonds melted into the steel edge. This makes them very hard. This process is called ‘sintered’ and these types of saws are used in a wide variety of applications.
Cutting the stone can become very messy because mineral oil is used to cool the stone and it splash and run everywhere.
It is, however, a necessary process because the vibrations of the saw and an unsteady hand may cause the stone to chip or even crack. If this happens the stone is worthless.
The rough shape is then ground into a more perfect one with a diamond grit wheel. This is quite dangerous and has often resulted in the jeweller nickering fingernails and fingers.
The next technique is called ‘dopping’. This requires the stone to be fixed to a rod using wax. This keeps the gemstone in place so more delicate work can be done on it.
Perfection takes time
A master jeweller would then grind away at the top of the stone to create a perfect dome. This has to be done by eyesight and touch and, as you can imagine, takes years to master.
The stone is then ground more on a belt made of silicon carbide. Other grits are used from rough to fine polish to get the best out of the stone.
In total there are over 12 stages of grinding and polishing one gemstone.
At the completion of this process, the stone is buffed with cerium oxide, a rare earth element. It is then ready to be set.
To learn how a master jeweller polishes a gemstone click here.